By Dr. Michael Bartholomeusz
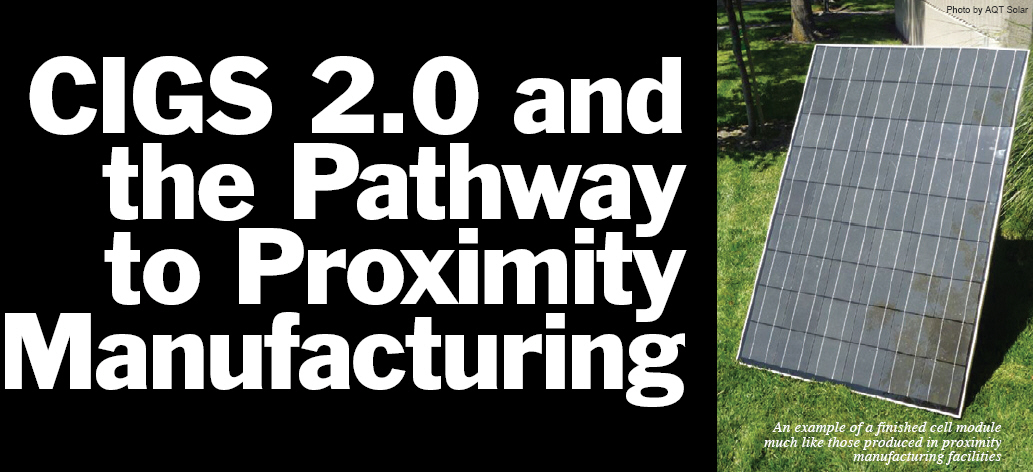
The Photovoltaic (PV) industry is poised for a radical shift. While traditional silicon cells have proven effective for decades, silicon is bumping up against inherent limitations, including thin-film efficiency challenges and slow energy payback. While the introduction of CIGS (Copper Indium Gallium Selenide) solar cells and modules offers an attractive lower-cost alternative to silicon, conventional CIGS manufacturing techniques and business processes have limited its commercial adoption.
Today, a new model for production and deployment, dubbed CIGS 2.0, a leverage-based approach that incorporates the three factors required by the new economy; rapid and cost-effective scalability, cost reduction and continuous technical advancement on flexible, future-proofed manufacturing platforms, can deliver an option that the solar industry, including more than 400 silicon module manufacturers, can embrace and deploy across the globe. The model also allows for the introduction of proximity manufacturing, whereby multiple manufacturing plants can be built regionally to meet the needs of those markets, while taking advantage of policy and subsidies created to support and sustain the solar industry in its infancy. The market for thin-film PV has the potential to grow substantially over the next few decades, and the CIGS 2.0 model is now poised to become a viable player in the PV industry.
Silicon solar cells have been the industry standard since its inception. Its sustained growth has encouraged the adoption and development of renewable energy systems utilizing solar. Silicon’s biggest challenge, which is rarely addressed, is exactly how much energy is required to produce those cells and panels. In fact, it’s such an energy intense process that it typically takes up to two to four years (depending on location) in a solar field for a single panel to pay back the electricity it took to manufacture that very panel. Additionally, thin-film silicon offers a lower-cost alternative, but its efficiency limitations require a greater number of modules, making it space prohibitive to deploy.
An Advantage and Weakness
CIGS avoids these silicon pitfalls. Payback often requires less than one year in the field to cover its energy production costs. CIGS is also low cost, like silicon, and could offer roughly the same energy efficiency as polysilicon panels. The materials required--copper, indium, gallium, selenide--are neither toxic nor especially rare, delivering a constant, affordable and safe source for thin-film solar cells. To date, however, the challenges associated with the widespread development, adoption and commercialization of CIGS solar cell technology center mainly around the approach companies have taken to, rather than the efficiency or costs of, its development.
For example, most existing manufacturers create CIGS utilizing multiple and discontinuous processes of Physical Vapor Deposition (PVD), Chemical Vapor Deposition (CVD) and Chemical Bath Deposition (CBD). This complicated technique is a proven process, but allows for little specialization or innovative device designs. Companies entering the CIGS market have also typically taken a greenfield approach, creating and building the actual manufacturing equipment. As a result, these CIGS manufacturers are now CIGS custom equipment manufacturers as well, needlessly forcing attendant start-up costs and risks upon themselves. In taking CIGS from the lab to market, these companies also must meet the difficult transition from small lab cells to large monolithic modules in a single step. And because they are now manufacturing entire modules, not simply solar cells, consistency across such a large area is difficult to maintain, which becomes a greater problem as these CIGS manufacturers are in direct competition with long-established silicon manufacturers.
CIGS 2.0: An Option

CIGS 2.0 avoids three of these difficult challenges and ultimately shares only one, the maturation of the single-step, all-dry sputtering of PVD. However, this single processing approach allows for greater specialization and the ability to custom design and size CIGS solar cells. Otherwise, the manufacturing platform adopted for CIGS 2.0 relies on existing equipment, developed and commercialized initially for the Hard Disk Drive (HDD) manufacturing market. The substrates in HDDs are similar in size to CIGS cells, offering CIGS 2.0 a proven, mature manufacturing platform with years of field production and performance behind it. The sputter deposition used in the HDD industry is what resulted in meeting Moore’s law for storage density.
In addition, rather than taking a module-based approach to manufacturing solar solutions, CIGS 2.0 creates individual solar cells. Upscaling to development requires minimal scaling (from 4-inch lab cells to 5-inch and 6-inch production cells). And those cells fit into the existing PV infrastructure.
Manufacturing Benefit
CIGS 2.0 gives rise to a new manufacturing model, where the plants built for solar cell production can be located regionally as PV projects demand. Proximity manufacturing is made possible in part because the machines required to make the CIGS 2.0 cells--the aforementioned HDD manufacturing equipment --are small, taking up just 214 square feet each. This translates to a much smaller incremental capacity--one line housed in a roughly 20,000 square foot site can have capacity as small as 15 MW and still maintain reasonable cost efficiencies.
Only conventional CIGS supersites, housing the relatively large manufacturing lines required to produce solar modules (as opposed to individual solar cells), were previously thought able to reach the economies of scale necessary to compete with silicon. CIGS 2.0, with medium-sized manufacturing sites located regionally, is projected to achieve economies of scale not previously seen in such a small footprint.
Proximity manufacturing offers several other market benefits as well. Today, and in the near term, PV will continue as a policy-driven industry. Subsidies, as well as tax breaks and other benefits for adopting renewable energy, will help solar get to a point of self-sufficiency. Until then, regions and countries will incentivize companies for local job creation and the establishment of PV manufacturing plants. A solution lending itself to proximity manufacturing allows each regional or country site to engage those job-creation credits, tax breaks and other incentives, while those regions obtain the benefits of new green industry jobs.
Ultimately, the cost of solar energy production will fall so that it is economically viable without this additional policy support. At that point, the cost of these PV components will be so low that shipping costs then become the significant portion of the total cost of solar deployment. By locating these smaller production sites in multiple regions and nearby developing solar projects, those shipping costs are then dramatically reduced, driving down solar expense even further.
Market with CIGS 2.0
CIGS offers a reasonable alternative to traditional silicon, especially as silicon’s true costs become evident as the market continues to expand and grow. However, companies hoping to take CIGS to market face four simultaneous challenges and often fall short on all four. Process, platform, scale and size must all be taken into consideration. CIGS proponents facing these challenges often run up against significant roadblocks in commercial and business success, particularly when taking on established silicon module manufacturers.
Simplifying the development process by adopting an all-dry sputtering deposition may be the key to potential rapid increases in efficiency, as well as the creation of new solar designs. Embracing a proven manufacturing platform from the HDD industry drastically reduces capital costs and investment risks, while upscaling cell size from lab to market is kept to a minimum. Finally, by manufacturing solar cells that fit into an existing solar module infrastructure, rather than complete modules, opens up silicon module makers as a market by offering them cell replacements and becoming an option for new products from established solar brands.
Each of these advances has also aided in the development in a new proximity manufacturing model for the PV industry, because smaller manufacturing sites become economically feasible for the first time. In the near term, proximity manufacturing allows CIGS 2.0 companies to benefit from multiple regional and country policies aimed at expanding renewable energy sources, while introducing new green manufacturing jobs into many additional regions. Once policy-based support for solar is no longer necessary, localized manufacturing will help drive down shipping costs to maintain price advantages, regardless of subsidies.
Michael Bartholomeusz, CEO and co-founder of AQT Solar (http://aqtsolar.com), has served in technology and executive capacities in aerospace, electronics and energy industries and has extensive expertise in global enterprise management. With over a dozen published patents he holds a Ph.D. in Materials Engineering from University of Virginia and Executive MBAs from The Darden School of Business and The St. Gallen Management Institute in Switzerland.
For more information, please send your e-mails to .
ⓒ2025 interpv.net All rights reserved.
|